A Comprehensive Guide to Efficient Warehouse Construction Planning
Understanding the Importance of Efficient Warehouse Construction
Efficient warehouse construction planning is crucial for businesses aiming to optimize logistics and storage capabilities. Proper planning not only enhances operational efficiency but also significantly reduces long-term costs. A well-constructed warehouse serves as a backbone for supply chain management, ensuring smooth operations and timely delivery of goods.
When embarking on a warehouse construction project, it's essential to consider factors such as location, size, and design. These elements play a pivotal role in meeting the specific needs of the business while accommodating future growth and technological advancements.

Key Factors in Planning Warehouse Construction
Location and Accessibility
Selecting the right location is the first step in warehouse construction planning. Consider proximity to major transportation hubs such as highways, railways, and ports. This ensures that goods can be moved efficiently, reducing transportation costs and time. Additionally, evaluate the availability of skilled labor in the area, as this can impact both construction and ongoing operations.
Design and Layout
The design and layout of a warehouse should be tailored to the specific needs of the business. Consider factors such as ceiling height, floor load capacity, and column spacing to maximize storage space and operational efficiency. Incorporating flexible design elements can accommodate changes in inventory types and volumes over time.
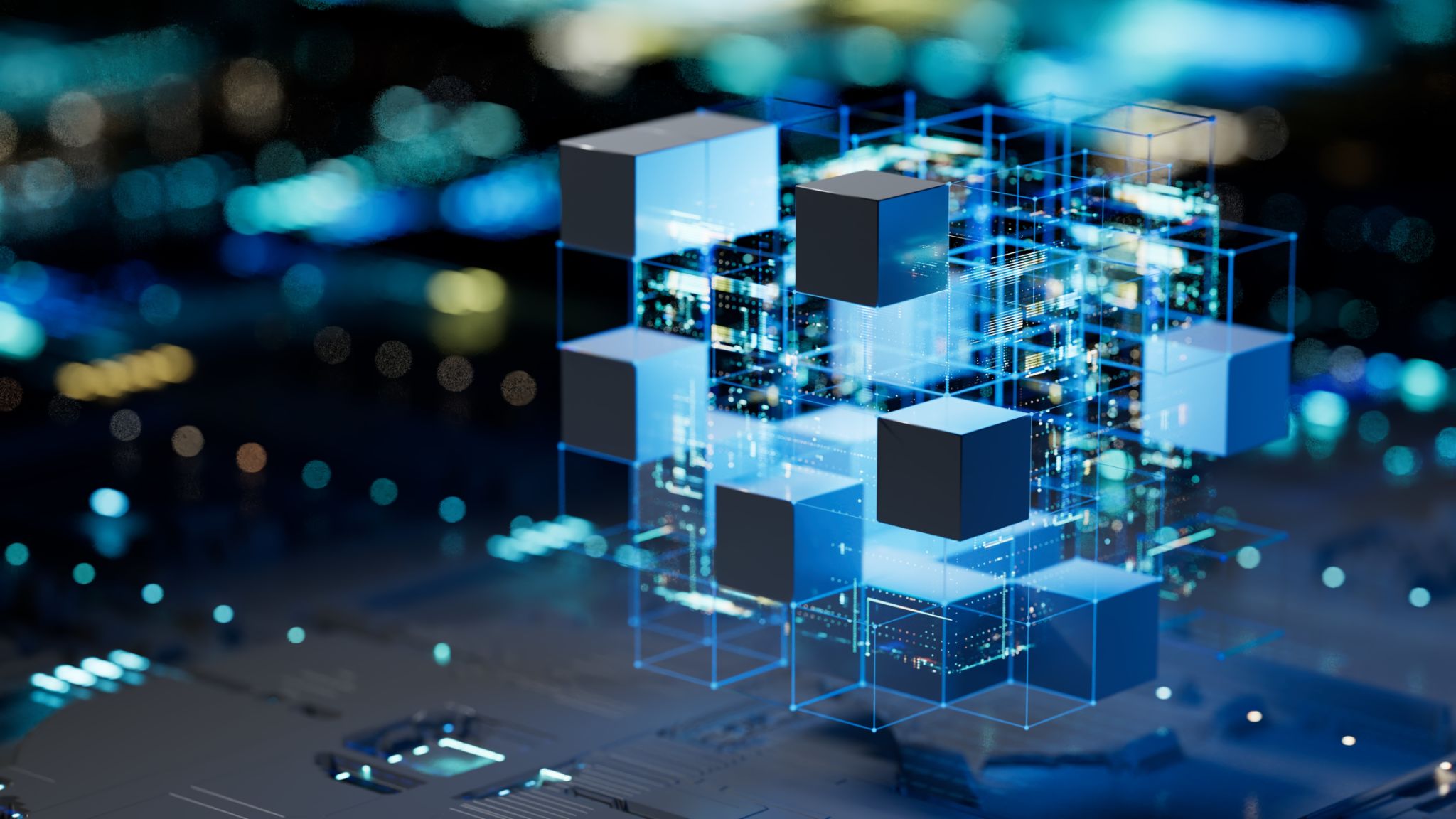
Incorporating Technology in Warehouse Construction
Automation and Robotics
Integrating automation and robotics into warehouse operations can significantly enhance efficiency. Automated systems for sorting, packing, and inventory management reduce human error and increase speed. Consider designing spaces that can accommodate such technologies from the outset to future-proof your facility.
Sustainable Building Practices
Sustainability is becoming increasingly important in warehouse construction. Implementing eco-friendly building materials and energy-efficient systems can reduce the environmental impact and lower operational costs. Consider installing solar panels or using natural lighting to decrease reliance on non-renewable energy sources.
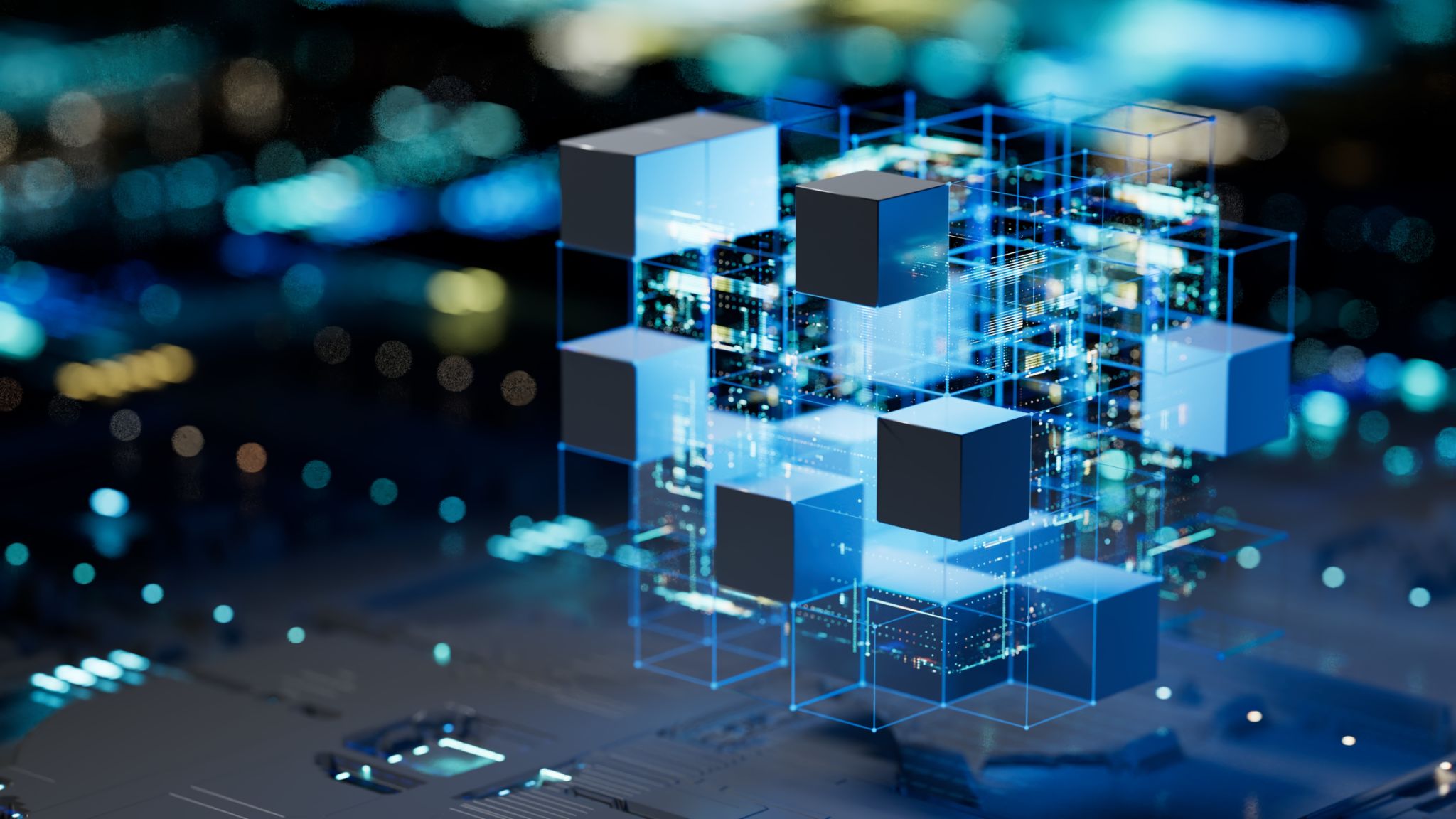
Managing Costs and Budget
Cost Estimation
A comprehensive budget is critical for the successful completion of a warehouse construction project. Start by estimating costs for land acquisition, materials, labor, and technology integration. It's important to include a contingency fund to cover unforeseen expenses that may arise during construction.
Project Management
Effective project management ensures that construction stays on schedule and within budget. Hiring experienced professionals who can coordinate between architects, contractors, and suppliers is essential. Regular progress reviews help identify potential issues early, allowing for timely adjustments.
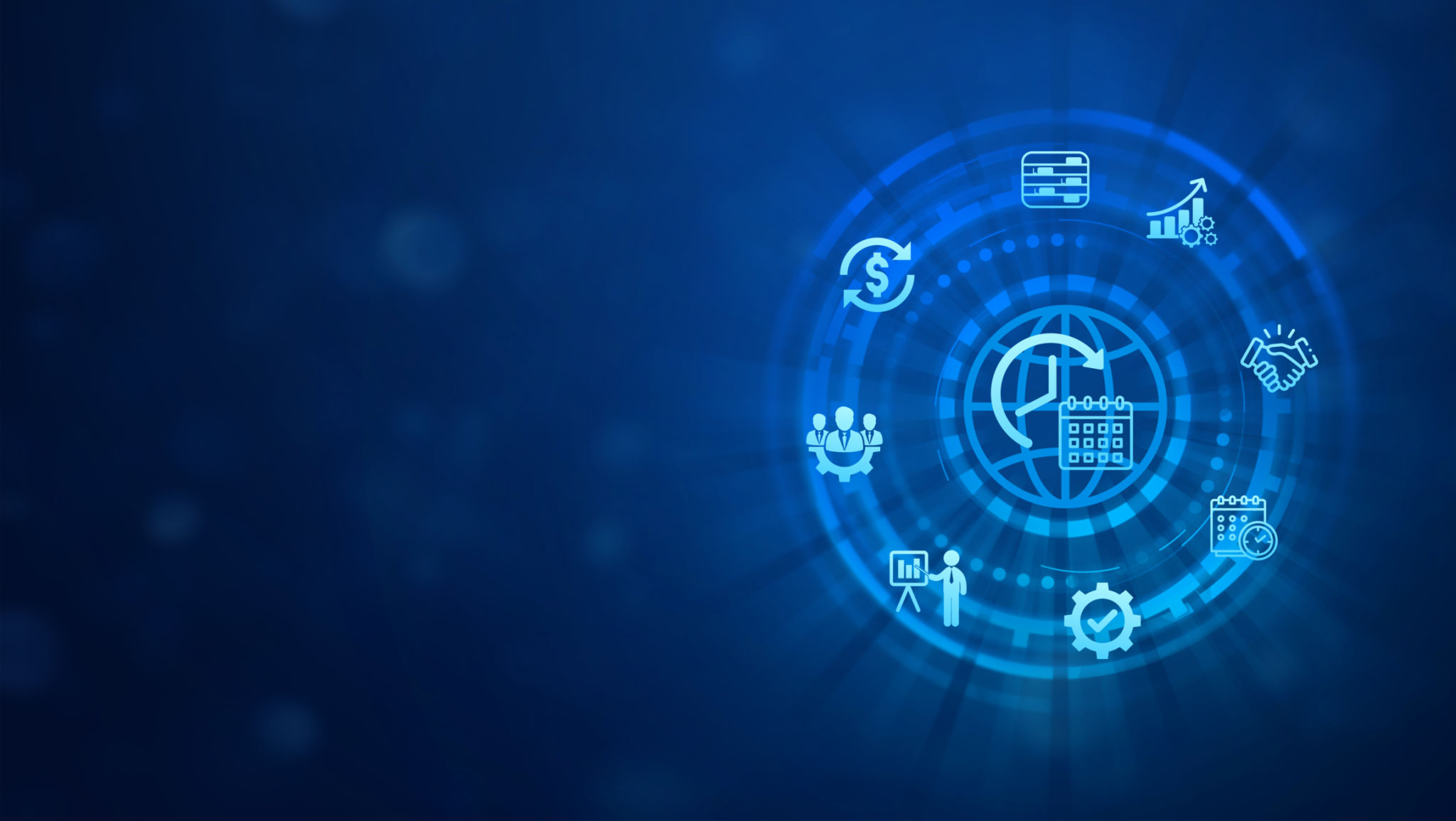
Ensuring Compliance and Safety
Compliance with local regulations and safety standards is non-negotiable in warehouse construction planning. Ensure that your design meets all zoning laws, building codes, and health and safety regulations. Investing in proper fire suppression systems and emergency protocols is crucial to safeguarding both employees and inventory.
By meticulously planning each phase of warehouse construction, businesses can create efficient, cost-effective facilities that support their operational goals. From selecting the right location to integrating advanced technologies, each decision plays a vital role in the overall success of the project.